The Role of Technicians in the Design of the Cascadia Results in More Uptime
Freightliner Trucks On-Highway Newsletter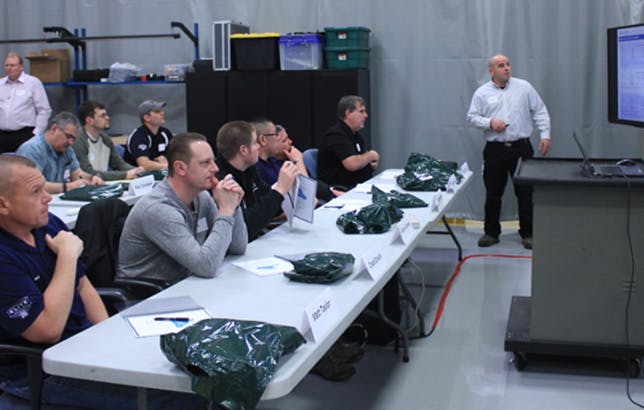
While designing the Cascadia, Freightliner hosted two Tech Week events where top technicians in North America were given a sneak peek of the new truck and were asked to provide feedback on its serviceability. Their comments and input resulted in technician-friendly changes to the design of the Cascadia.
“We wanted to get information and feedback from the folks who work on trucks all the time, and incorporate that into the design process,” said Greg Nightingale, the aftermarket new product development manager at Daimler.
The first Tech Week event in 2015 included a 72-point inspection of the current Cascadia® compared to the Cascadia prototype built for the event, classroom work, and mock repair procedures using the new components. Technicians provided feedback that was presented to the chief engineers at Freightliner.
“The initial feedback on the design was really positive,” said Nightingale. “The technicians had some ideas to make it even better, and they were very willing to be a part of that process.”
Here are some of the changes that were made to the Cascadia based on technician feedback:
- Easily removable bumper: With technician input, the bumper comes off in about two minutes andan be installed or removed by one person.
- Redesigned HVAC outside cowl piece: Removal is improved and provides easier access to the engine. The blower motor was made smaller and positioned for easier access, and the top dash panel can be removed more efficiently.
- User-friendly electronic vault (eVault): The Cascadia has a central location for access to and troubleshooting the electronic control units (ECUs), which is a huge improvement in serviceability. It also allows easy removal of ECUs and modules and allows technicians to back-probe. The antilock braking system (ABS) ECU in the eVault has become more accessible, and the routing of the airlines is much cleaner.
- Informative instrument cluster functionality: The screens and indicators were improved to show fault code severity with two different messages: “Service now” and “Service later,” and you can scroll through fault code displays.
- Streamline cable routing: Cable routing and clipping is neater and more user-friendly, which increases the routing quality and consistency of air lines, fuel lines, and electrical harnessing that runs under and back of the cab.
In the second Tech Week in 2016, technicians reviewed and validated the changes made to the Cascadia based on their feedback. Freightliner also hosted a competition where technicians were split into teams, tasked with finding purposely placed bugs in the Cascadia’s electronic system, and then fixing them.
Based on the success of Tech Week, Nightingale says Freightliner will continue including technicians in its product development. “Technicians have a wealth of information. It’s been a real positive message, and it’s certainly been a central theme in the rollout of the Cascadia.”